What is Superforming?
Superforming is a manufacturing process which utilizes the characteristics of certain aluminum, magnesium and titanium alloys to elongate several hundred percent when subjected to controlled strain rates at elevated temperatures. Only specific types of metals exhibit the properties to stretch 1000% before fracture. These metals require a fine uniform grain structure and can be formed to have complex, double curvature shapes.
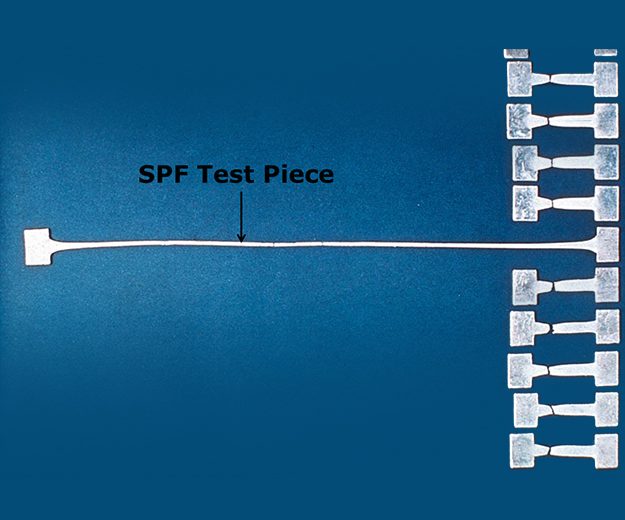
Our Process
Superform USA specializes in a variety of forming processes ranging from Cavity, Bubble, Diaphragm to Back Pressure forming. Across all techniques, we follow the following method:
- A metal sheet is clamped and heated in a hot press
- A single-surface tool is used to force the sheet against the tool surface to provide the required shape
- Part is subsequently trimmed and other value-added processes incorporated as required
This process is derived from one of our key strengths, which is the unique design capabilities we possess for SPF. We strive to work with our customer during the design phase to ensure the desired end result is accomplished. Whether it be from a multi-piece assembly turned into a single forming to a weight reduction exercise, utilizing our SPF technology helps achieve an array of solutions for your needs.
All tooling is design engineered in-house, utilizing Catia V5 as well as tool proofing through our Finite Element Analysis Software (PAM-STAMP) ensuring feasibility of parts before entering the press!
This enables Superform to produce parts and minimize tooling costs at a fraction of the time and price compared to conventional tool stamping dies.
Check out our Process in Action
Our Capabilities
Superform USA’s equipment and process capabilities include:
- Computer controlled Superplastic Forming Presses
- CNC 5-axis machining centers
- Prima Industries Optima Laser 5-axis Trim center
- Chemical Cleaning System
- Welding Operation
- Detail Product Assembly
- CATIA and Mastercam seats
- PAM-STAMP forming simulation software
- Inspection Systems including two 6-axis ROMER arms with Verisurf inspection software and a Horizontal Arm CMM using PC-DMIS
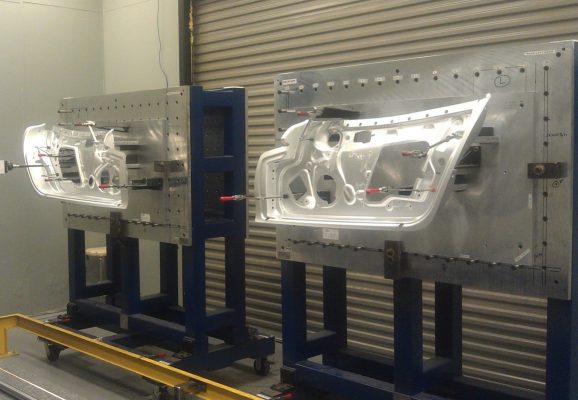